摘 要 研究了不同龄期受损混凝土经过相同养护期后的自然愈合现象.混凝土受损后的自愈合实质上是损伤部位未水化或水化不充分的胶凝材料加速水化或进一步水化生成新的水化产物弥合裂缝的过程.以超声波速的变化表征混凝土受压开裂后的损伤程度,建立了混凝土损伤量与愈合状况之间的关系.结果表明,混凝土材料存在一个损伤阈值:当混凝土的损伤低于损伤阈值时,自愈合率随着损伤量的增大而增大;当混凝土损伤超过损伤阈值时,自愈合率随着损伤量的增大而降低.
关键词 无机非金属材料,混凝土,损伤,自愈合,水化
在水泥混凝土的使用过程中,温、湿度的变化、不均匀沉陷或外加(动、静)荷载引起的直接应力以及次应力等原因,都可能导致混凝土的开裂.裂缝的存在及其发展,不仅影响到混凝土结构的正常使用性能和耐久性,而且危及结构的安全.但是,并非所有的初始裂缝都会演变为有害的或失稳的裂缝.J.Stefan(1995)发现,将混凝土试件冻融破坏之后放置一段时间后,混凝土恢复了一部分共振频率,并且在裂纹中有钙矾石晶体和氢氧化钙晶体.有些防水结构的裂缝(宽0.1~ 0.2 mm,经过一段时间后完全封闭.有些学者甚至发现宽度0.3 mm的裂缝经过一段时间后都可以完全恢复.一些研究表明:受损混凝土的力学性能在相当大的程度上都可以恢复,但是这种自愈合能力取决于多方面因素,包括混凝土的组成,受损时的龄期,自愈合的环境条件(湿度,温度)以及愈合期等.同时,混凝土的受损程度也是影响自愈合效果的重要因素.虽然宽度0.1~ 0.3 mm的裂缝能够愈合,但是实际上绝大多数的裂缝最终导致结构物的破坏.如何定量表征混凝土的自愈合过程?本文研究混凝土自愈合过程的损伤修复及其机理.
1 实验方法
主要实验用材料有:ISO~32.5普硅水泥,I级粉煤灰,中砂(石子最大粒径31.5 mm),萘系减水剂和聚丙烯腈微细纤维(表1)。
为了使实验结果具有代表性,配制了纤维混凝土和素混凝土,其配合比列于表2。新拌混凝土的坍落度为(200±20)mm.成型立方体试件的尺寸为100 m m *100 mm *100 mm 。
为了区分在不同龄期受损对混凝土愈合的影响,加载实验中分别选择养护7 d,14 d,28 d龄期的混凝土。将加载开裂的试件放入温度20℃、相对湿度95% 的养护室中养护30 d。进行超声实验前将试件从养护室后在通风良好处放置2 h,以使其含水率基本一致.实验中用穿透法对试件进行探伤分析。一个方向的损伤不仅与本方向的波速降低线性相关,还与另外两个方向的波速降低线性相关。因此,采用对测法用CTS一25型非金属超声波检测仪测量侧向超声波速在加载前后的变化,加载方向和测量超声波速方向垂直。
2 结果与讨论
从表3可以看出,随着未损伤混凝土强度的提高,穿过混凝土的超声波速度也随之提高.但是在强度较低(例如10~15 MPa)时,穿过混凝土的超声波声速变化的规律性比较差(图1).因为超声波声速的变化能反映出物体的基本物理性质,如物体孔洞、裂缝、密度等,可用于检测混凝土的强度、孔洞、裂缝等.但是,由于声速与混凝土密度、弹性模量等有密切关系,与强度只有相关关系,不能单独使用超声波波速的绝对量来检验.
混凝土试件经过30 d的自愈合之后,不仅其力学性能有所恢复,超声波速也有不同程度的恢复(图2).在初始损伤之后超声波速较大的混凝土试件在愈合30 d之后超声波速仍然较大,损伤后和愈合后的超声波速具有比较好的一致性.这表明,用超声波声速比值的变化可以比较好的表示混凝土材料的受损状况.
混凝土的超声波速主要决定于其弹性参数.将混凝土视为宏观裂缝、分散微裂区和具有稳定缺陷的基体组成的复合材料.在混凝土承受荷载前后,具有稳定缺陷的基体的变形是线弹性的,其弹性常数保持不变,因而对混凝土的声学特性没有影响;而微裂隙在单轴受荷后的变形(闭合、张开、扩展等)会引起混凝土的弹性常数改变,因而是改变混凝土声学特性的主要因素;宏观裂缝是在承受荷载之后出现的,也是影响混凝土材料超声波速的一个重要因素.混凝土的整体超声波速是三个因素的耦合作用的结果.对于在受载条件下的脆性固体材料,声学特性研究结果表明:若假定其母质具有线弹性,在其内部随机分布了大量微裂纹,则声速随单轴应力呈非线性变化关系. 这种关系可以简略的表示为 VP=g(
,σ 1),其中VP 为超声波传播速度; = (E0,v ,KIc,φ ,ao,α,∈),其中Eo,v 分别为母体的弹性模量和泊松比,KIc,φ分别为材料的断裂韧度和内摩擦角,a0,α,∈分别为微裂纹半长度、形状比和裂纹密度;σ 1为单轴应力.

本文所研究的混凝土的超声波速仅限于受载前后和自愈合之后,可以不考虑受载时应力对波速的影响.这样,超声波速的变化与材料母体的弹性模量、泊松比、断裂韧度、内摩擦角、微裂纹半长度、形状比和裂纹密度等细观参数有关.混凝土超声波速应为超声在基体,微裂区,宏观裂缝三相中传播速度的组合效应,可表示为
,其中 Vc为超声波在混凝土中的传播速度, i1, i2, i3和V1 ,V2 ,V3分别为基体、微裂区和宏观裂缝在混凝土中的体积分数以及超声波在三者中的传播速度.其中V3 即为超声波在空气中的速度340 m/s,V1=
1(Eo,v ,KIc,φ),V2=
2(ao,α,∈),其中Eo、KIc的增大将导致V1 的增大,ao,α,∈的增大则导致V2 的减小.
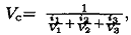


在混凝土加载之前,超声波在混凝土中的传播速度主要取决于V1,基体的弹性参数影响超声波在混凝土中的传播速度,混凝土的强度越高,其弹性模量较大,超声波速也越大.但是声速还与V2 有关(完好混凝土试件i3=0),并非完全随强度线性变化(图1).当混凝土受载损伤后,内部的一些初始微裂纹发展成宏观裂纹,同时又产生大量的微裂纹,完好基体所占比例i1急剧减少,i2,i3则相应增加;同时微裂区内的a0,α和∈增大,导致超声波在微裂区传播速度减小.因此,受损后材料的超声波速急剧下降.受损后的混凝土自然养护30 d后,由于未水化和未完全水化水泥颗粒的进一步水化,重新生成的水化产物将填充在裂缝处.J.Stefan看到在微裂缝边缘有明显的生成产物,并且新的水化产物在裂缝的边缘最为密实,在裂缝中央部分则稀疏.新水化物的填充减小了宏观裂缝的宽度,i3减小.同时水化产物在微裂纹中生成一方面减小了i 2,另一方面改善了混凝土裂缝的结构,使a0,α,∈均减小,从而导致在微裂纹区中超声波的速度增大.因此,自愈合后的混凝土超声波速上升很快,有些试件愈合后的超声波速甚至超过了受载之前的超声波速,如0#-2,1#-3.
由于超声波速与材料内部的细观结构密切相关,超声波速的变化能反映材料内部微损伤区的变化.为了建立损伤程度与混凝土自愈合程度之间的定量关系,定义材料受载前后超声波速衰减的相对值为混凝土的损伤D=1一v/v0 和材料愈合后抗压强度的增量与未损伤时抗压强度的比值为混凝土的自愈合率H=(Sh-S)/S,其中D为材料的损伤,v 为受载后材料的超声波速,v0为受载前材料的超声波速,H为材料的愈合率,Sh 为愈合后材料的抗压强度,S为不同龄期受损时的抗压强度.
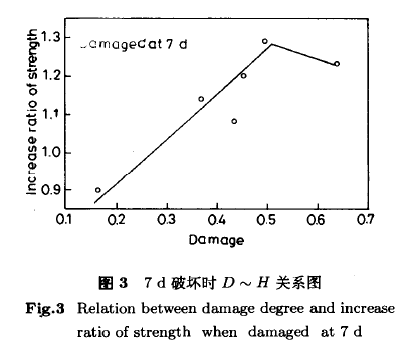
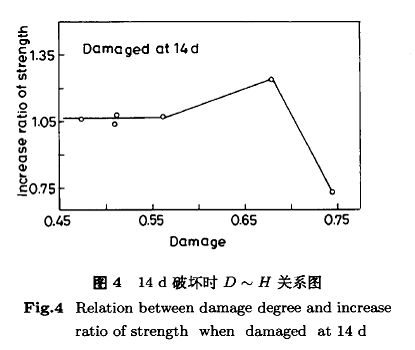
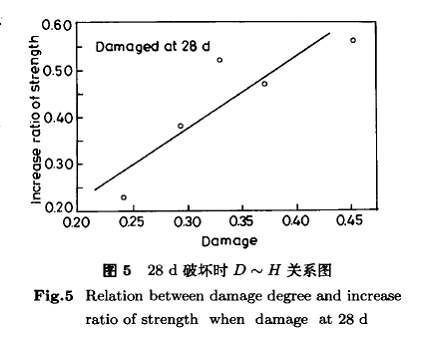
混凝土材料损伤程度较低时其愈合率也较低,如D=0.16时(图3).随着损伤程度的增大,混凝土相应的强度增长率提高,但是当D>0.6之后材料的强度增长率稍有下降.当D>0.7时混凝土的愈合率大幅度下降,而损伤为0.45 ~0.55时材料的愈合率基本持平(图4).损伤0.2~ 0.5时,D~ H关系比较一致,愈合率基本上随着损伤的增大而增大(图5).这些结果说明,混凝土材料在愈合时存在着损伤的阈值:超过了损伤阈值材料的愈合率会大大降低,而损伤小于损伤阈值时,材料的愈合率随着损伤的增大而增大,而不是随着损伤的增大而减小.其原因可能是:混凝土自愈合的一个最主要原因是混凝土中未水化的水泥颗粒的进一步水化.在受损过程中混凝土的内部产生大量的微细裂纹,可能导致大量被水化产物包裹的未水化水泥颗粒暴露出来.在潮湿环境中,这些未水化水泥颗粒进一步水化,填补了因受损而产生的微细裂缝.若损伤过小,能够暴露的未水化水泥颗粒数量较少,不利于混凝土的自愈合;但是若损伤超过一定限度,新的水化产物不能完全填充受损裂缝,导致愈合率大幅度下降.
图3~ 5表明,混凝土的受载龄期对自愈合效果有显著的影响.在损伤程度相同的情况下,早龄期受损的混凝土自愈合能力更好.在早龄期,混凝土内部还存在大量未水化的水泥颗粒,能够修复损伤和继续提高强度.
3 结 论
受损伤的混凝土存在自愈合能力,自愈合有一个损伤阈值. 当混凝土损伤小于损伤阈值时,材料的自愈合率随着损伤的增大而增大;当损伤超过损伤阈值,材料的自愈合率随着损伤的增大而减小.以承受荷载前后超声波速的变化来表征混凝土的损伤程度,本文研究的混凝土损伤阈值为0.6~ 0.7。